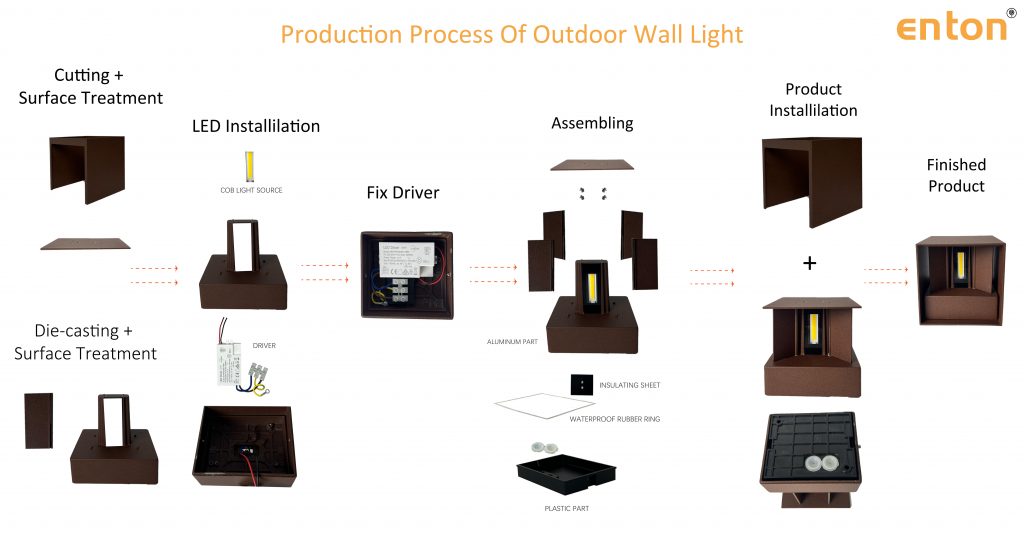
The sales team at Enton Light has created a outdoor wall light production process. The structure of this light is somewhat complex, as it contains multiple components made from different materials and requires various processing steps. Therefore, it serves as an excellent example to illustrate the lamp production process.
This wall lamp is composed of seven parts: 1. Aluminum housing, 2. Plastic bottom cover, 3. Waterproof sealing cover, 4. COB light source, 5. Driver, 6. Terminal block, 7. Fasteners.
Regarding the aluminum housing, some parts with more complex structures are formed through die casting, while simpler parts are made by cutting aluminum plates directly purchased from the market. Finally, these parts undergo surface treatment together. Generally speaking, the more complex the structure, the more difficult it is to form, and the higher the mold cost.
The bottom cover is a plastic component produced through the injection molding process. Injection molding is a common process for making small plastic parts, some large parts will use blowing molding or rotational molding. Large lighting factories usually have their own injection molding equipment, while medium and small-sized factories may outsource this component to other suppliers. Once the mold is completed, the production speed of injection molded parts is rapid, but the minimum order quantity can be relatively high.
The waterproof sealing cover is a standard part that we can purchase directly from the market, which greatly saves time and cost.
The light source and driver are usually procured together from external suppliers. For this lamp, the COB light source has a relatively unique shape. However, most light sources are produced by large domestic manufacturers, who typically have stock available. For this slightly special COB light source, it may take around 15-25 days, depending on the quantity required.
Once all the parts are ready, the factory workers assemble the product. The COB and light source are connected via the terminal block. After the internal assembly is complete, to achieve an outdoor waterproof rating of IP54 or above, the sealing areas are filled with glue, and the product is finally secured with fasteners. This completes the production of the outdoor wall lamp.
Next, we conduct a final lighting test to ensure the customer does not receive defective products. If any defects are found, we analyze the cause and rework the product. Only after passing the test is the product shipped to our customers.
If you have any needs in this regard, please contact the Enton sales team!